Back to Applications
Logistics & Automation
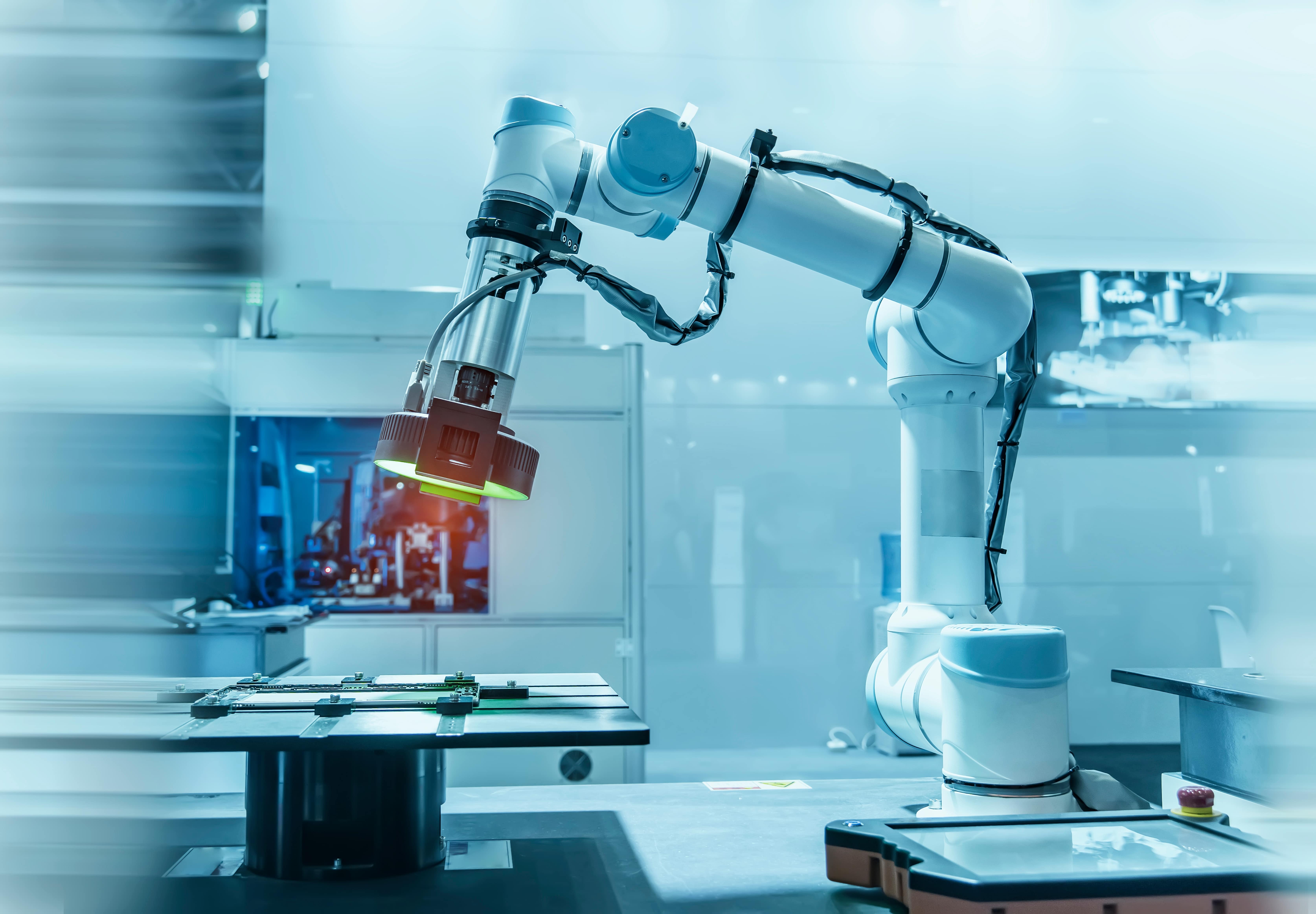
Robotics
Machine vision commonly provides location and orientation information to a robot to allow the robot to properly grasp the product. This capability is also used to guide motion that is simpler than robots, such as a 1 or 2 axis motion controller. The overall process includes planning the details of the requirements and project, and then creating a solution. Many of the process steps are the same as with automatic inspection except with a focus on providing position and orientation information as the result.
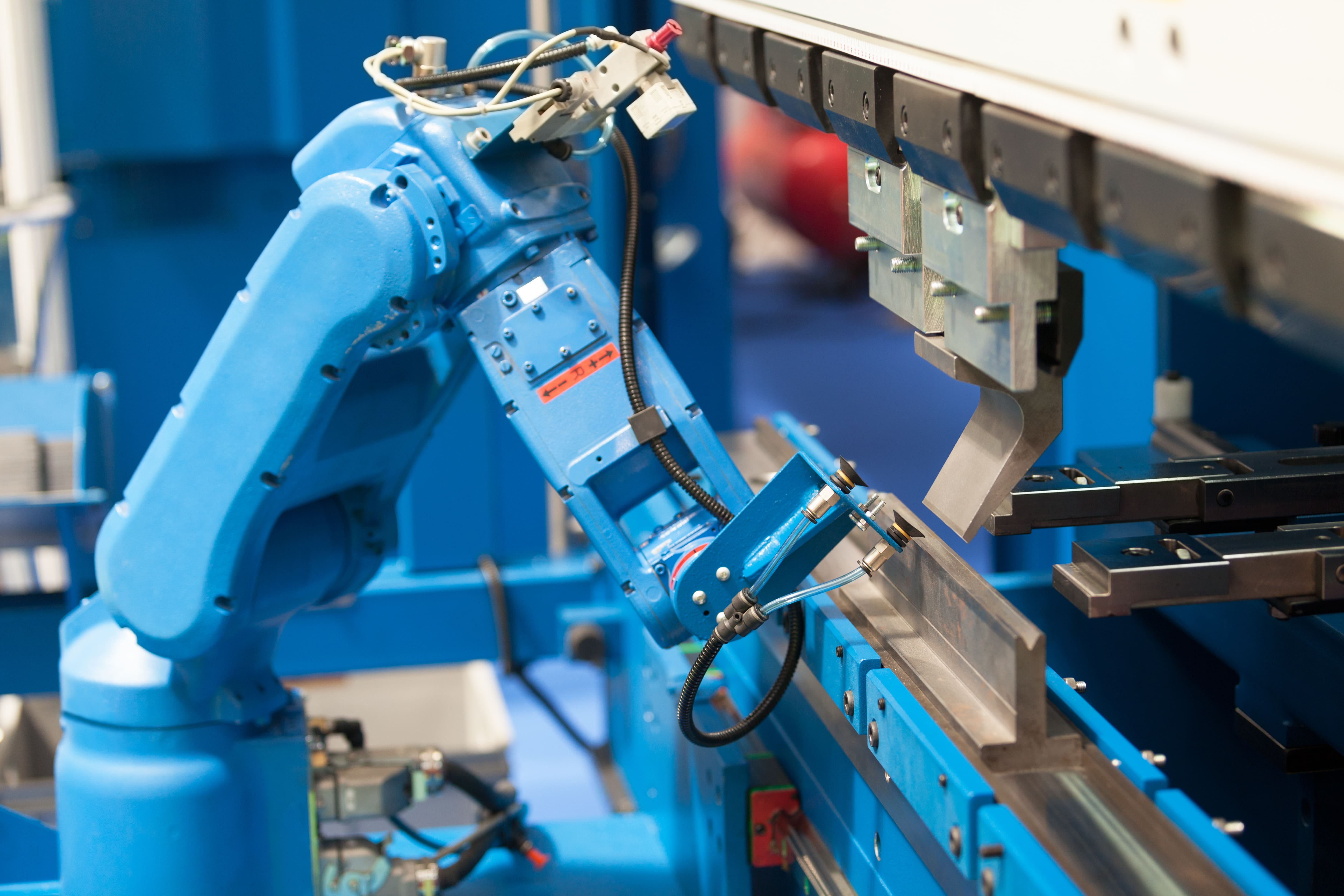
Pick & Place
Machine vision cameras are essential components in pick and place systems, revolutionizing automated manufacturing processes by enabling precise and efficient handling of parts and components. These cameras are mounted above conveyor belts or robotic arms, capturing high-resolution images of the work area. Equipped with advanced image processing algorithms, machine vision cameras analyze these images to identify and locate objects with pinpoint accuracy. In pick and place systems, cameras determine the position, orientation, and characteristics of parts, guiding robotic arms or manipulators to accurately grasp and place them onto designated locations. By providing real-time feedback and precise control over the picking and placing process, machine vision cameras enhance speed, accuracy, and flexibility in manufacturing operations. Additionally, with the integration of machine learning techniques, these cameras can adapt to variations in part geometry or appearance, further optimizing pick and place operations in diverse industrial environments. Overall, machine vision cameras play a crucial role in automating pick and place tasks, increasing productivity, and reducing labor costs in manufacturing industries.
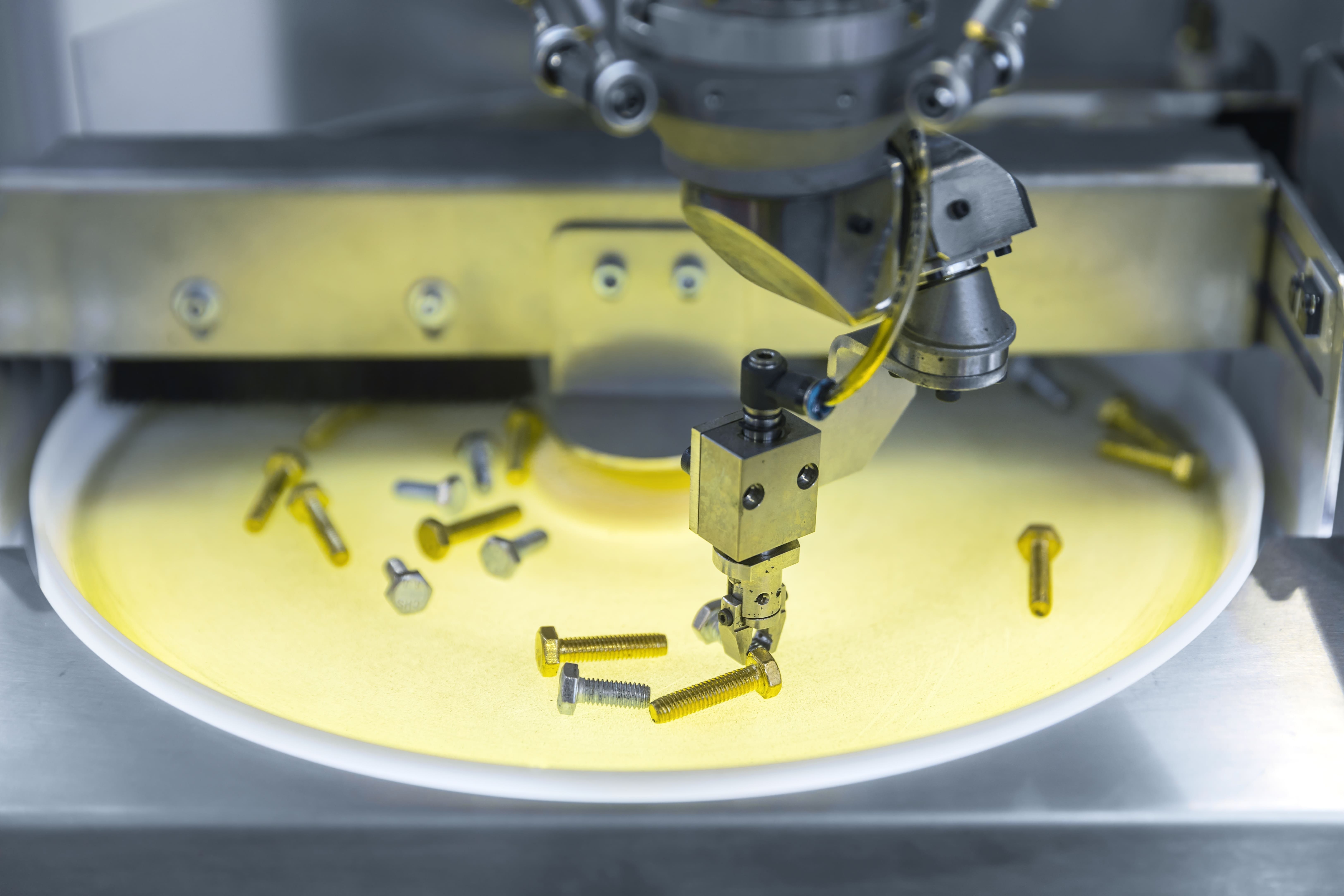
Parts Handling
Machine vision cameras are integral components in parts handling systems, facilitating efficient and accurate manipulation of components and products in various industrial processes. These cameras, equipped with high-resolution sensors and advanced image processing capabilities, are strategically positioned to capture detailed images of the work area. In parts handling systems, machine vision cameras analyze these images to identify, locate, and inspect parts with precision. This information is then used to guide robotic arms, conveyors, or other automated equipment to handle the parts according to predefined criteria, such as sorting, orienting, or assembling them. By providing real-time feedback and precise control over the handling process, machine vision cameras optimize throughput, minimize errors, and ensure consistent quality in manufacturing operations. Additionally, with the integration of machine learning algorithms, these cameras can adapt to changes in part geometry or appearance, further enhancing the flexibility and efficiency of parts handling systems across various industrial applications. Overall, machine vision cameras play a vital role in automating parts handling tasks, improving productivity, and streamlining production workflows in modern manufacturing facilities.
Models We Recommend